Position:
/
Our Vacuum Casting Services
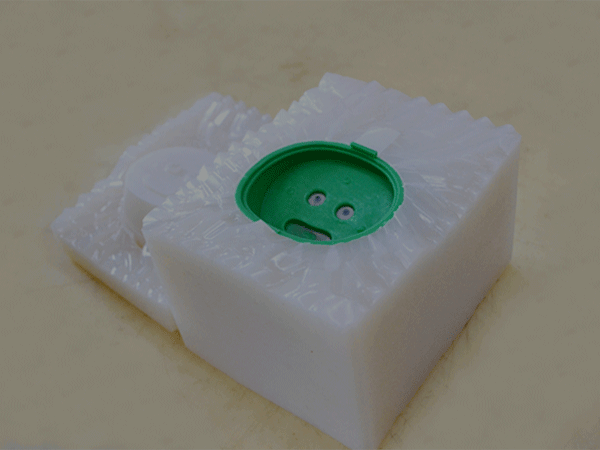
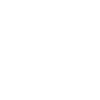
Vacuum casting (also known as RTV molding, cast urethane, and silicone molding) is a fabrication method that uses silicone molds to produce production-quality plastic parts.
Vacuum Casting production consists of three main steps:
1. Build a master pattern using 3D printing or CNC machining
2. Build the mold by pouring platinum silicone around master
3. Pour liquid polyurethane resin into mold, create polyurethane casting under vacuum
Request A Quote
Vacuum Casting Tolerances
Typically Vacuum Casting Part Tolerances
Description
Tolerance Notes
Distance Dimensions
+/- 0.010” or +/- 0.003” per inch, whichever is larger, is typical. Irregular or overly-thick geometries may cause deviances or deflection due to shrinkage.
Shrink Mitigation
A shrinkage rate of +0.15% can be expected due to thermal expansion of the liquid, and the response of the flexible mold.
Surface Quality
Surface finish is externally smoothed to a satin or matte surface. Grow lines may be present on internal or difficult-to-access features. Polishing or custom finishes must be clearly defined and agreed upon at the point of order.
Feature Definition
Sharp corners and text may appear slightly rounded.
Size Recommendation
We can offer vacuum cast parts as large as 30” (0.762 m) long.
Advantages of Vacuum Casting
Urethane casting has a low-cost and quick turnaround for high-quality plastic parts compared to injection molding or 3D printing. Where injection molding requires an expensive upfront investment for the machining of the mold, the silicone mold required for urethane casting is inexpensive and easy to produce. Additionally, while most 3D printing processes require extensive post-processing to get to a near-finished state, urethane cast parts come out of the mold ready to go. Urethane casting is an excellent choice for creating high-quality prototypes or low-volume production of rigid, flexible, clear, colored, or rubber-like plastic parts.
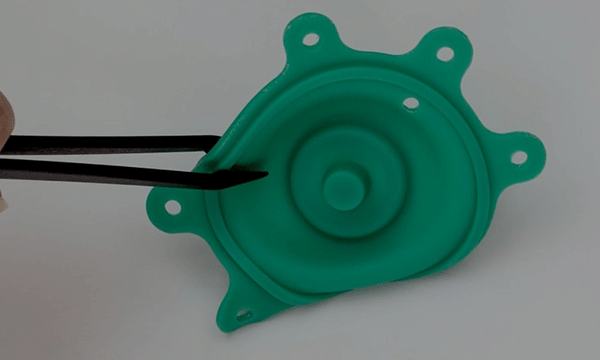
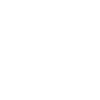

Low tooling costs

Self coloured parts

Surface textures

Fast and allows for design iteration

Minimal redesign required

Undercuts OK, draft not required
Request A Quote
OUR EXPERIENCE IN NUMBERS
12,000 sq/m Manufacturing Facility
More than 30 years of industry experience
Serving customers in more than 100 countries
More than 100 3D printing equipment
More than 300 cnc processiong equipment
Vacuum Casting Materials
NAME
DESCRIPTION
DETAILS
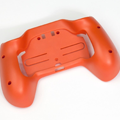
NAME
ABS-Like
DESCRIPTION
ABS-Like is a general purpose polyurethane plastic that simulates ABS thermoplastic. This material is a great choice for most product enclosures.
DETAILS
$$
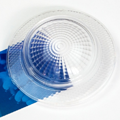
NAME
Acrylic-Like
DESCRIPTION
Acrylic-Like is a stiff, transparent polyurethane plastic that simulates acrylic (PMMA). This material is great for see-through applications such as light pipes.
DETAILS
$$$$
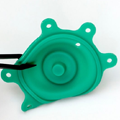
NAME
Opaque Elastomereel
DESCRIPTION
Opaque Elastomer is a polyurethane plastic that simulates all kinds of rubber-like materials such as TPE, TPU, and silicone rubber.
DETAILS
$

NAME
Waterclear Elastomer
DESCRIPTION
Waterclear Elastomer is a urethane casting material that simulates all kinds of rubber-like materials such as TPE, TPU, and silicone rubber.
DETAILS
$$$
Vacuum Casting Surface Finishes
PAINTING
Painting refers to the surface coating processing of industrial products. Spray the specified color according to the customer's requirements.
Applicable Materials : ABS-Like, Acrylic-like, Opaque Elastomer
Color : Any RAL code or Pantone number
Texture : Uniform gloss or matte
Function : Improve the appearance of the product, and extend the service life of the product through an extra layer of protection.
Learn More >>
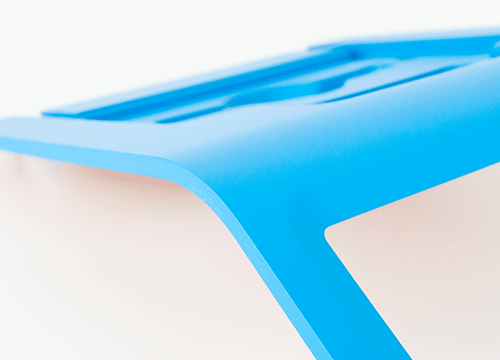
Contact Sales

Design guidelines for Vacuum Casting
TIPS & TRICKS
Remove undercuts if possiblece
Specify a lower grade surface finish
Mold in standard plastics–pp, abs etc
Reduce weight of part.
Specify a lower grade surface finish
Mold in standard plastics–pp, abs etc
Reduce weight of part.
TOLERANCES
± 0.5mm or ± 0.1mm/30mm whichever is greater.
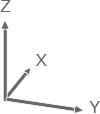
WALL THICKNESS
Varied wall thicknesses are allowed but consistency is recommended. HLH suggests a minimum wall thickness of > 1mm.
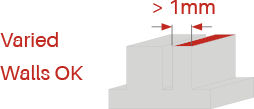
UNDERCUTS
Not a problem for vacuum casting and can be done without inserts.
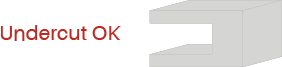
RIBS
Ribs should be ≤ 60% of the wall thickness to reduce sink, include as large a radius as can be tolerated.
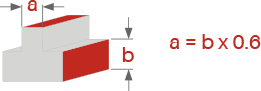
TEXT & LOGOS
Recessed or embossed. Text should be ≥ 1mm wide and deep/high and for best result with a 1mm gap between letters.
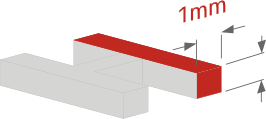
HOLES & BOSSES
Through holes are easy, blind holes less so but can be molded. Threaded inserts via over mold or post process. Bosses should have a minimum height and diameter of > 1mm. Bottom radius ≤ 25% of wall thickness and the walls of the boss ≤ 60% to prevent shrink.
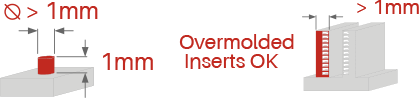