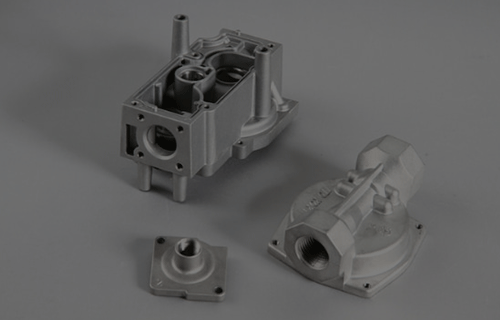
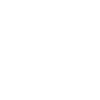
Hot chamber die casting, also known as gooseneck casting, is a considerably quick process with a typical casting cycle only 15 to 20 minutes. It allows for high volume manufacturing of comparatively complex parts.
The process is ideal for zinc alloy, lean alloys, copper and other alloys with low melting point.
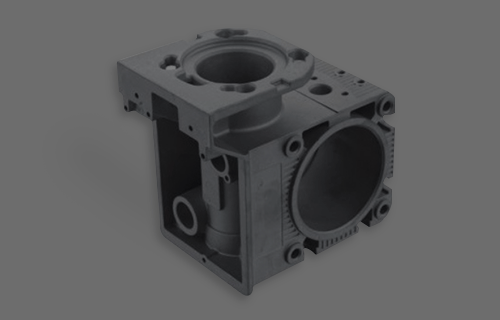
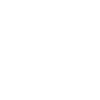
Cold chamber die casting process is an very important procedure which helps reduce the amount of heat and solve the corrosion problem in machine's plunder and related components.
The process is primarily used for alloys with high melting points, like aluminum, magnesium, some copper, and ferrous alloys.
OUR EXPERIENCE IN NUMBERS
12,000 sq/m Manufacturing Facility
More than 30 years of industry experience
Serving customers in more than 100 countries
More than 100 3D printing equipment
More than 300 cnc processiong equipment
Die Casting Materials
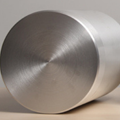
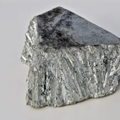
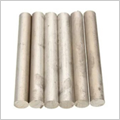
Die Casting Surface Finishes
Sandblasting is the process of cleaning and roughening the surface of the substrate by the impact of high-speed sand flow. Due to the impact and cutting effect of abrasives on the surface of the product, the surface of the product can obtain a certain degree of cleanliness and different roughness.
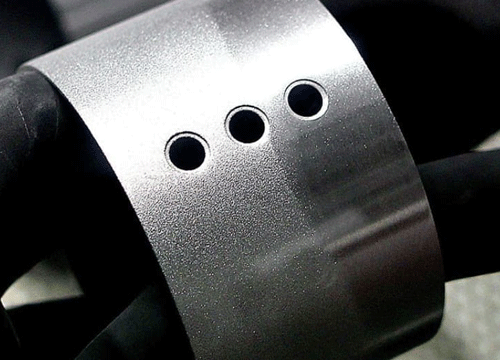
Applications of Die Casting
Automotive Parts
We specialize in making vehicle parts like gears, cylinders, gladhands, transfer cases, small engine parts, and components for lawn and garden tractors.
Aerospace Industry
Our magnesium and aluminum pressure die casting service can produce light, durable structural parts for aerospace with great resistance to corrosion.
Telecommunication Components
Produce electrical enclosures, connector housings, heat sinks, and many more components.
Contact Sales

Step 1: Prepare mold. You need to heat the mold to a specific temperature and then spray the interiors of the mold with a refractory coating or lubricant.
Step 2: Inject material. After the solid metal alloy is melted into a liquid state, pour molten metal into the mold under a required pressure.
Step 3: Cool the metal. Once the molten metal is injected into the cavity, take sufficient time to let it harden so that it can form the shape of the mold.
Step 4: Unclamp the mold. Next, unclamp the mold carefully and take out the cast part.
Step 5: Trim the casting part. The last step is to trim sharp edges and excess material to make the desired component shape.